Progressive Cavity Pump: Working Principle, Applications, and Benefits
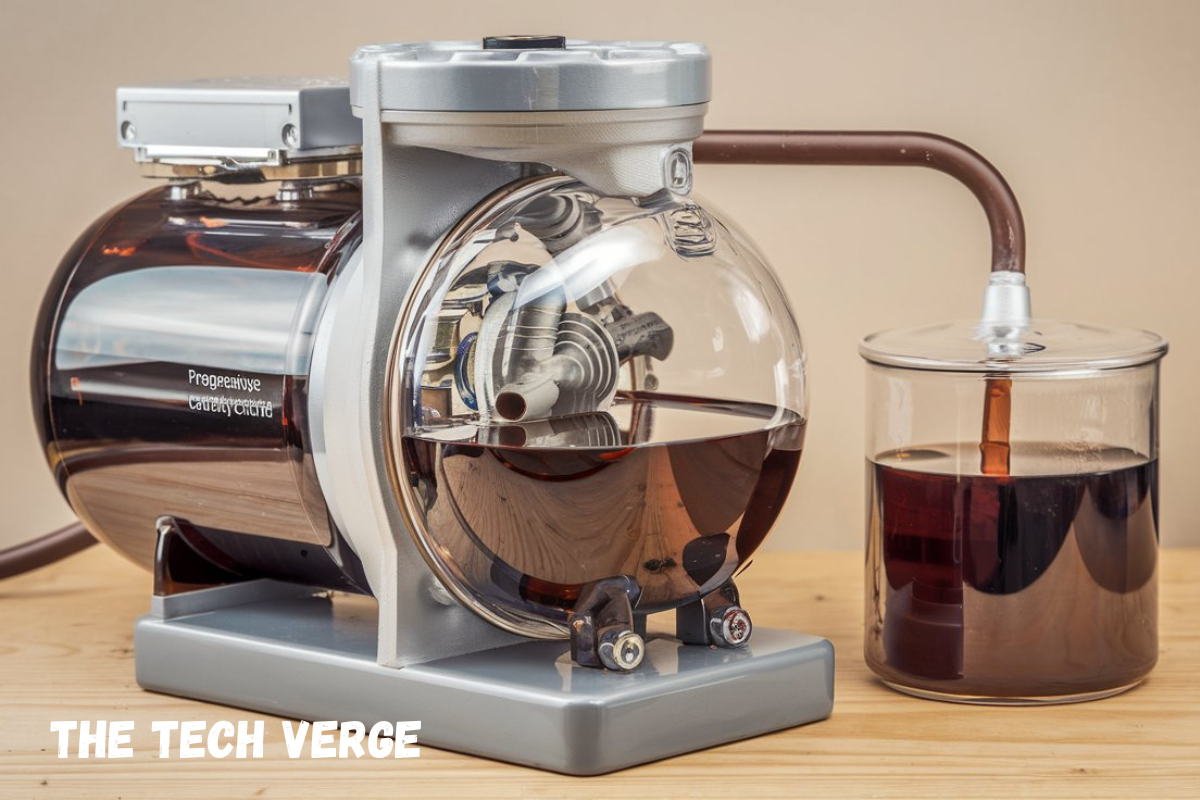
Oil and gas, wastewater treatment, and food processing are just a few of the industries that use the progressive cavity pump, a flexible and effective positive displacement pump. This pump is an essential tool in many industries because of its reputation for handling sensitive materials, slurries, and viscous fluids.
This article explores the working principle of progressive cavity pumps, compares them with centrifugal pumps, highlights their key advantages and disadvantages, and answers common questions like “What is a it used for?” and “How does a it work?”
What is a Progressive Cavity Pump?
A progressive cavity pump (PCP), a type of positive displacement pump, moves fluids through a series of small, fixed cavities as the rotor rotates inside a helical stator.
Key Features:
- Progressive cavity pumps handle abrasive materials and high-viscosity fluids effectively.
- Gives off a steady, non-pulsing flow.
- Ideal for moving fluids that are delicate or sensitive to shear.
- Able to manage fluids that contain solids.
See also: New Technology in Drone Manufacturing: Revolutionizing the Skies
How Does a Progressive Cavity Pump Work?
- Rotor and Stator Interaction: Within an elastomeric stator, a helical rotor turns to create sealed cavities.
- Fluid Movement: These chambers gradually travel along the stator as the rotor rotates, transporting the fluid from the suction side to the discharge side.
- Constant Flow Rate: Even when the pressure changes, the flow rate stays constant.
Working Principle of a Progressive Cavity Pump
The coordinated motion of an elastomeric stator and a helical rotor forms the basis of the progressive cavity pump’s operation.
- Suction Phase: Fluid is drawn into the pump by the vacuum created by the rotor’s spinning.
- Sealed Cavities: The cavities created between the stator and rotor trap fluid.
- Fluid Transfer: From the suction end to the discharge end, the fluid gradually travels.
- Discharge Phase: The fluid is released by the pump at a steady flow rate.
Advantages of the Working Principle:
- Minimal fluid shearing.
- Pumping action for delicate textiles is gentle.
- Dependable management of abrasive and high-viscosity fluids.
Progressive Cavity Pump vs. Centrifugal Pump
Knowing how these two pumps differ from one another aids in choosing the appropriate machinery for a given application.
Feature | Progressive Cavity Pump | Centrifugal Pump |
Fluid Type | Viscous, abrasive, shear-sensitive fluids | Thin, clean fluids |
Flow Rate | Constant flow rate | Flow rate varies with pressure |
Pressure Handling | Effective at high pressures | Limited pressure capability |
Shear Sensitivity | Gentle on fluids | Can damage shear-sensitive fluids |
Applications | Oil, wastewater, food processing | Water circulation, HVAC systems |
Which One to Choose?
- For fluids that are thick, viscous, or abrasive, use a progressive cavity pump.
- For the movement of thin, clean, or massive volumes of fluid, opt for a centrifugal pump.
See Also: Typewriter Keyboard: Retro Charm Meets Modern Tech
Applications of Progressive Cavity Pumps
Progressive cavity pumps are highly versatile and used across multiple industries.
- Oil and Gas: Managing drilling muds, viscous petroleum products, and crude oil.
- Wastewater Treatment: Involves moving heavy debris, slurries, and sludge.
- Food and Beverage: Shearing-free pumping of dairy products, syrups, and sauces.
- Chemical Processing: Transporting extremely caustic and viscous substances.
- Agriculture: Fertilizer transfer and irrigation.
Example: The Seepex Pump, a top manufacturer of progressive cavity technology, is frequently utilized in wastewater treatment to transfer sludge effectively.
Advantages of Progressive Cavity Pumps
- Easily manages abrasive and high-viscosity fluids.
- Ensures steady and even fluid flow.
- Ideal for delicate and shear-sensitive goods.
- Performs well at high pressure.
- Able to prime itself.
Disadvantages of Progressive Cavity Pumps
- Increased maintenance expenses as a result of stator and rotor wear.
- Restricted to specific degrees of chemical and thermal resistance.
- Reduced effectiveness when using fluids with low viscosity.
- Requires exact alignment when being installed..
Conclusion
A very effective and adaptable pump for handling viscous, abrasive, and delicate fluids in a variety of sectors is the progressive cavity pump. It remains a popular option in situations when other pumps might not be sufficient due to its distinct operating principle and capacity to maintain a steady flow rate.
Knowing its benefits, drawbacks, and best uses guarantees the equipment’s longevity and best use.
See Also: Nuances of Cybersecurity: Key Concepts, Types, and Strategies
FAQs
What is a Progressive Cavity Pump?
A progressive cavity pump transfers high-viscosity, shear-sensitive, and solids-laden fluids through a series of sealed cavities as a positive displacement pump.
What is the Difference Between a Progressive Cavity Pump and a Centrifugal Pump?
Cavity pumps handle viscous fluids and offer constant flow, while centrifugal pumps are better for thin, clean fluids with varying flow rates.
What are the Disadvantages of a Progressive Cavity Pump?
Users face higher maintenance costs, limitations with low-viscosity fluids, and the need for precise installation when using these pumps.
What Are Progressive Cavity Pumps Used For?
Industries like oil and gas, wastewater treatment, food processing, and chemical manufacturing rely on progressive cavity pumps.
What is a Seepex Pump Used For?
Industries like wastewater treatment and food processing use Seepex pumps primarily to transfer sludge, thick fluids, and shear-sensitive products.